Packaging films protect food items from moisture, germs and other external contaminants. They also protect the quality of products and prolong their shelf life. Choosing the right film for your product is dependent on several factors, including its physical capacity and availability.
Flexible film is highly customizable based on the shape, size and visual needs of your product. It can help you save on production costs and deliver a competitive advantage.
Stretch film is a heavy-duty plastic wrap used to keep product boxes locked on to their pallets and reduce costly damage during shipping. It’s available in different widths and colors to meet the needs of your packaging operations.
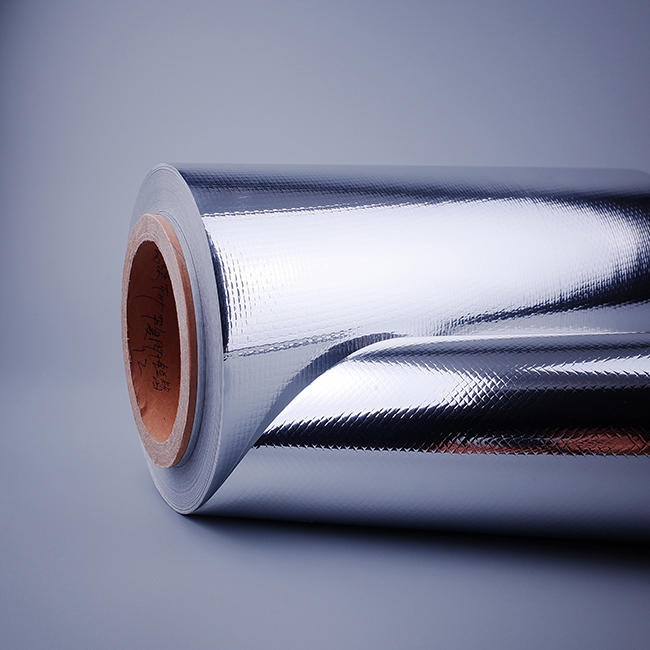
Stretch film manufacturers produce stretch films through a process called extrusion. Initially, the resin mix is heated until it becomes molten and then forced through a flat die to begin the cooling and shaping process.
Machine grade stretch film is manufactured through a cast extrusion process and typically has better clarity, less force required to stretch, higher tear resistance, unwinds quietly from machines, and offers superior cling. Machine-grade stretch film is primarily available in blown and cast varieties.
Choosing the right gauge and thickness of stretch film is crucial to a successful packaging operation. Many stretch film users attempt to save money by down-gauging, but this can lead to expensive product damage and unnecessary wear and tear on your machine and equipment.
BOPA films are available in a variety of thicknesses and formats. They can be used to package products such as ready-to-eat food, processed foods, and fresh fruits and vegetables. The growing demand for these products will drive market growth.
PP is used to produce many forms of packaging. It is a major material in the film market, with applications for food and confectioneries, as well as tobacco products. It is also widely used in rigid packaging such as containers, caps and closures. In addition, PP is used in the manufacture of pallets and crates that are easy to transport, stack and re-use.
Unlike some plastics, PP is non-toxic and has very low environmental impact. It is also highly moisture-resistant and has good stiffness. PP can be made into a variety of shapes through the use of various conversion processes such as injection molding, extrusion and blowing.
PP is also used in the medical industry due to its excellent chemical and bacterial resistance. It can withstand stringent sterilization procedures. It also has great electrical resistance, which makes it ideal for manufacturing electrical components. Moreover, PP is economical and easy to process. It is recyclable without hurting the environment, which makes it a great choice for manufacturers.